Evolutions techniques saison 2019
Préparation au Orthez-Béarn 2019
5) Modification des trains roulants Voilà LA seconde raison principale de toutes les modifications et travaux attaqués durant l'inter-saison (et le début de saison). Après avoir changé le moteur de sens, deux autres aspects seront parmis ceux qui feront le plus progresser le comportement du véhicule :
1- L'augmentation significative des débattements aux 4 roues
2- L'augmentation sensible de la voie et de l'empattement
Concernant les débattements :
Notre point de départ est un train avant à 250mm de débattement avec un ratio 50% détente / 50% compression. Le train arrière est bloqué à 220mm de débattement princialement à cause de la course limitée des amortisseurs ainsi que d'une impossibilité physique d'aller plus loin en compression à cause de la conception du châssis ainsi que de la longueur des barreaux de transmission déjà "rallongés" artificiellement (voir ici). Nous avons 150mm de compression et 70mm de détente.
L'objectif est d'homogénéiser les débattements et de les augmenter tout en retrouvant des ratios plus standards dans le milieu du tout terrain. Ainsi, les trains avant et arrière voient leur débattement passer à 300mm avec 200mm de compression et 100mm de détente. Les ratios débattement/course amortisseur sont également revus et corrigés suivant les préconisations du fournisseurs des amotisseurs : P2S. Concernant la voie et l'empattement : Encore une fois, les dimensions de notre point de départ sont plutôt faibles. Avec un empattement de 2 340 mm et une voie de seulement 1 470 mm (largeur maxie de 1 670 mm), nous sommes bien en dessous des standards de la quasie intégralité des véhicules maintenant présents sur les plateaux.
Dépendant des travaux sur les transmissions (voir chapitre sur la transmission) ainsi que nos moyens de transport (remorque), nous limitons volontairement notre largeur maximale à 1 800 mm, ce qui nous fait retomber sur une dimension plus conforme aux standards. L'empattement sera augmenté en conséquence pour passer de 2 340 mm à 2 430 mm pour plus de confort en ligne droite. Nous ne voulons pas éxagérer l'augmentation d'empattement pour garder une voiture relativement vive et avec un look conforme à ce qu'il a toujours été depuis des années maintenant. 5-1 : Fabrication de nouveaux triangles Les éléments du train avant qui nous permettront d'atteindre ces objectifs sont les triangles. La double triangulation est bien sûr conservée. Longtemps au coeur des discussions, les supports supérieurs d'amortisseurs sont finalement conservés (même si celui de droite devra être reconstruit suite à ma sortie de route au D&M 2018).
Plusieurs facteurs influencent la conception des triangles et vont dicter leurs caractéristiques :
1- La largeur maximale doit passer de 1 670 mm à 1 800 mm
2- Les jantes en 16'' auront un déport de 50 mm, contre 25 mm avec les 504
3- Un usinage sur les moyeux de 504 (remplacant des R30 à l'avant) vont eux aussi envoyer les roues vers l'intérieur du buggy. L'objectif étant de réduire le dépot au sol pour se rapprocher du neutre.
4- La course des amortisseurs doivent suivre un ratio de 1.5 par rapport au débattement à la roue tout en gardant nos support supérieurs côté châssis
5- La tenue mécanique : les triangles doivent être au moins aussi solides que la génération précédente.
6- La masses des triangles devra rester proche deq existants. Réduire la masse sera compliqué étant donnés les augmentations de dimensions prévus.
A partir de ces éléments, plusieurs caractéristiques "intuitives" dirigent la conception :
1- L'allongement des triangles devra être de (1 800 - 1 670)/2 + (50 - 25) + ep usinage (10mm) = environ +100 mm . Cela nous donne une distance pivot - rotule connue à quelques millimètres près.
2- Le support d'amortisseur côté triangle devra être le plus bas possible. Nos avons besoin de 200 mm de course amortisseur. Pour se faire, la longueur détendue de l'amortisseur doit être maximisée pour loger une bute hydraulique additionnelle.
3- Si le support d'amortisseur est trop proche du milieu du triangle, les efforts de flexion rendront l'ensemble vulnérable au moindre talonnage. Réduire la distance rotule - pivot amortisseur est donc primordiale. Elle devra être minimale pour maximiser la résistance du triangle inférieur.
Après quelques passes de calcul et de conception CAO, des données se dégagent et permettent de tester des configurations en réel. Deux faux triangles sont conçus pour vérifier que la CAO se vérifie bien dans l'atelier. Les carrossage, l'évolution de la longueur des amortisseurs, les angles des rotules etc.. Il esont réglables sur plusieurs degrès de liberté pour trouver des solutions convenables :
L'évolution est assez nette :
A partir de ces "faux triangles" (supérieur et inférieur), des "marbres" de soudure sont construits petit à petit et permettront de créer les triangles originaux mais également de reconstruire si besoin est dans le futur.
Ces "marbres" restent relativement sommaires mais très efficaces pour positionner les éléments les un par rapport aux autres, respecter les entraxes et les angles des triangles :
Le triangle inférieur reçoit la suspension. Il sera donc soumis à des efforts importants en flexion et se doit d'être "costauds" pour encaisser les efforts, notamment lors des phases de compression et de freinage.
La structure tubulaire va se voire greffer une tôle pliée sur sa partie inférieure. Cette tôle, placée en dessous du plan de symétrie de la base tubulaire viendra se tendre dans les phases de compression et amener une bon rapport masse/rigidité. Les efforts supportés sont équivalent à ceux que seuls des tubes épais et de gros diamètre, plus lourds, auraient été capables de reprendre.
Cette opération est relativement compliquée sans plieuse et demande un peu d'imagination pour allier précision et netteté des pliages. A partir du modèle 3D, un patron su papier permet de rapidement sortir une version en carton pour valider la découpe de la plaque acier :
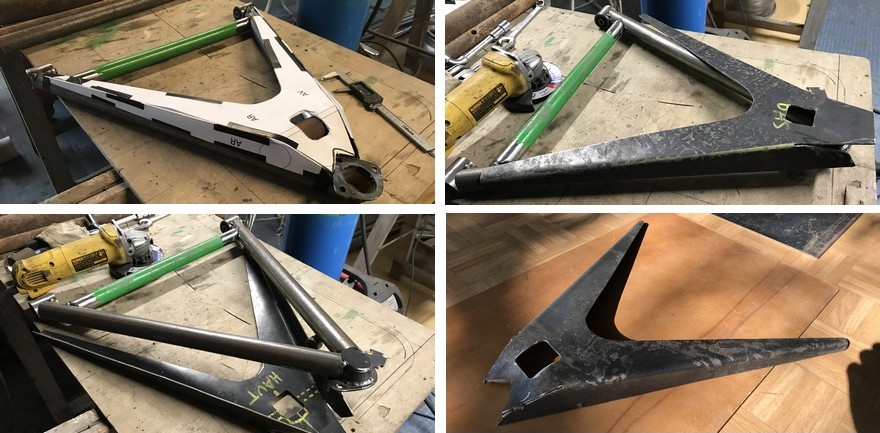
Grâce au marbre, les éléments sont positionnés et prêts à être pointés. Des essais sont ensuite effectués pour vérifier que nous respectons toujours les carrossages, voie et empattement au millimètre. Patience est le maître mot pour faire un travail aussi soigné que possible.
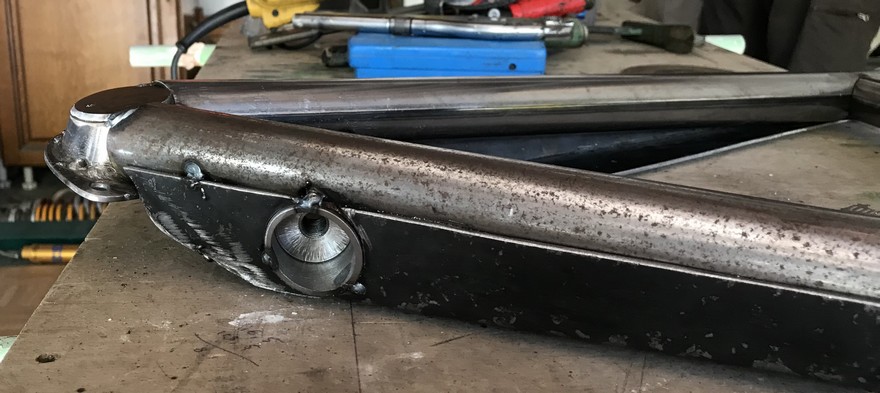
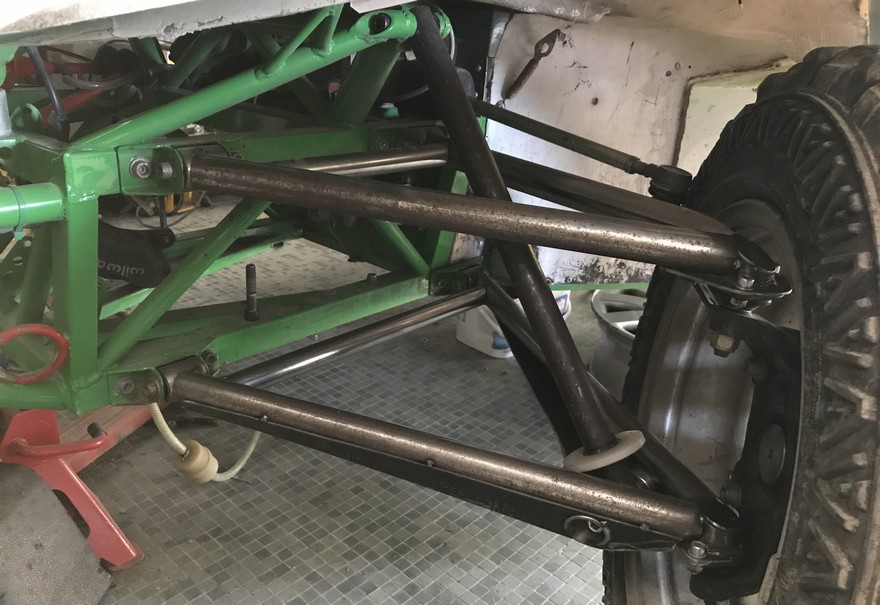
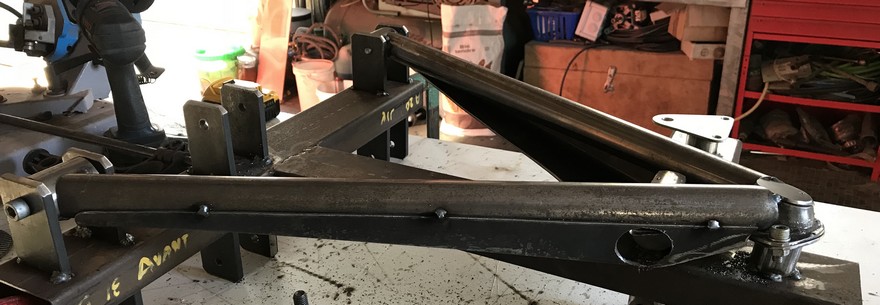
Après grenaillage et de longues heures de soudure, les voici dégraissés et prêts à passer enfin en peinture. Une ligne de moins sur le planning...
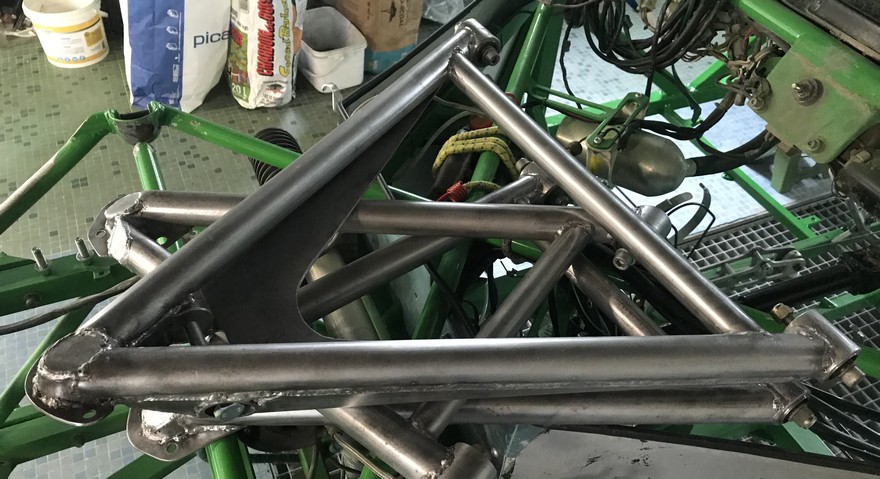